Every industry factors in corrosion protection, yet many businesses still lose millions annually to metal degradation. Why? Because they either underestimate how corrosion spreads or overinvest in the wrong solutions.
Corrosion isn’t just rust on the surface—it’s an active, electrochemical process that compromises metal from within. A single untreated flaw can escalate into structural failures, energy inefficiencies, and unexpected downtime. The real challenge isn’t just stopping corrosion but doing it cost-effectively.
The key isn’t using the most expensive coatings or treatments—it’s about applying the right protection for the right conditions. This guide explores proven, budget-friendly strategies for extending metal’s lifespan without excessive spending.
1. How Corrosion Quietly Increases Your Operating Costs
Most businesses assume they’re managing corrosion—until the hidden costs surface:
- Higher Energy Usage – Corroded pipes, machinery, and heat exchangers reduce efficiency, increasing power consumption.
- Increased Maintenance & Part Replacements – Weakening metal structures lead to frequent, costly repairs.
- Production Downtime & Compliance Issues – Unexpected failures result in delays and potential safety violations.
Proactive corrosion prevention isn’t an expense—it’s an investment that reduces long-term costs. The challenge is choosing cost-effective solutions that match your industry’s environment and exposure risks.
2. Why Some Metals Rust Faster Than Others (And What You Can Do About It)
Corrosion rates vary dramatically based on metal composition, environmental exposure, and industrial conditions:
- Chloride-rich environments (Coastal & Marine Industries) – Stainless steel isn’t fully corrosion-proof; pitting corrosion occurs if the passive layer is compromised.
- High-temperature settings (Oil & Gas, Power Plants) – Oxidation accelerates at extreme temperatures, leading to metal fatigue and scaling.
- Industrial pollutants (Chemical Plants, Manufacturing Units) – Acidic gases and airborne contaminants form highly aggressive corrosion cells on exposed surfaces.
Choosing the right corrosion protection isn’t just about coatings—it’s about understanding how metal interacts with its surroundings.
3. The 3-Tier Approach to Corrosion Prevention: What Really Works?
Protecting metal surfaces isn’t about overengineering solutions—it’s about choosing the right level of protection for the risk involved. Industries that manage corrosion cost-effectively follow a three-tier approach, combining surface protection, chemical treatment, and environmental control.
Tier 1: Surface Coatings – The First Line of Defence
Coatings create a physical barrier between metal and corrosive elements, but choosing the wrong type leads to premature failure.
- Powder Coating – Highly durable and chemical-resistant but not ideal for extreme heat or submerged environments.
- Galvanization (Zinc Coating) – Best for structural steel but can be compromised by scratches or acidic exposure.
- Industrial Paints & Epoxies – Effective in moderate conditions but require precise surface preparation for longevity.
✔ Cost-Saving Tip: Coating failure often occurs due to poor adhesion. Pre-treating metal with chemical solutions enhances bonding, reducing early degradation.
Tier 2: Chemical Treatments – Strengthening Metal at the Molecular Level
Chemical solutions don’t just protect the surface—they alter metal properties to resist corrosion from within.
- Phosphate Coatings – Create a corrosion-resistant layer that improves paint adhesion.
- Rust Converters – Chemically transform iron oxide (rust) into a stable, non-corrosive layer.
- Passivation for Stainless Steel – Removes free iron from the surface, reducing pitting corrosion in aggressive environments.
✔ Cost-Saving Tip: Using low-maintenance chemical pre-treatments extends the life of coatings, reducing the need for frequent reapplications.
Tier 3: Environmental & Design Controls – Stopping Corrosion Before It Starts
Most industries overlook simple, low-cost design changes that drastically slow corrosion.
- Drainage & Ventilation – Prevents moisture buildup that leads to crevice corrosion.
- Cathodic Protection in Harsh Environments – A low-cost electrochemical method that prevents rust from forming in pipelines and submerged structures.
- Avoiding Mixed Metal Assemblies – Using incompatible metals (e.g., aluminium and steel) creates galvanic corrosion, accelerating damage.
✔ Cost-Saving Tip: A minor design tweak—like avoiding water-trapping crevices—can double the lifespan of metal components.
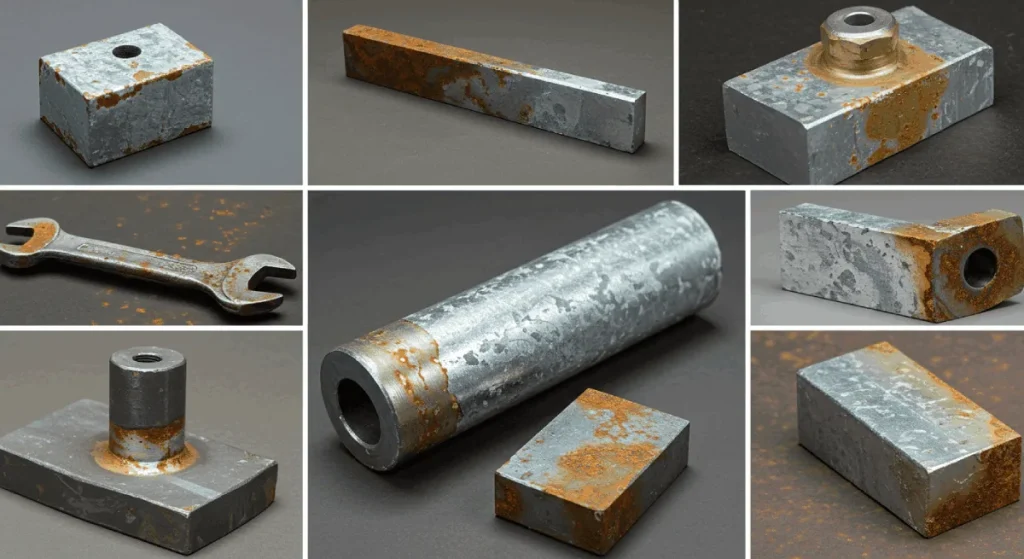
4. Protective Coatings: Are You Using the Right One or Just Wasting Money?
Coatings are one of the most widely used and cost-effective methods to prevent corrosion—but only when chosen and applied correctly. The wrong coating can lead to premature failure, unnecessary reapplications, and increased maintenance costs. The key is to match the coating to the specific environmental conditions.
Why Some Coatings Fail Faster Than Expected
- Using Standard Paint for Harsh Environments
- Issue: Industrial paints may protect against mild exposure but fail under constant humidity, salt, or chemical fumes.
- Better Alternative: High-performance epoxies or polyurethane coatings provide superior resistance in corrosive industrial settings.
- Assuming Galvanization is Always Enough
- Issue: While zinc coatings protect steel, they degrade rapidly in acidic or high-chloride environments.
- Better Alternative: Duplex coatings (galvanization + topcoat) extend durability in marine and industrial chemical applications.
- Skipping Surface Pre-Treatment
- Issue: Poor surface preparation leads to poor adhesion, early coating failure, and corrosion beneath the surface.
- Better Alternative: Pre-treating with Chembond’s metal treatment chemicals enhances coating adhesion and longevity.
Chembond Material Technologies: Providing Industry-Specific Coating Solutions
In industries where metal exposure conditions vary widely—from marine salt exposure to aggressive chemical processing plants—a one-size-fits-all approach to coatings doesn’t work. Chembond Material Technologies supplies industry-specific coating solutions that:
- Improve adhesion with advanced pre-treatment chemicals.
- Enhance corrosion resistance using scientifically formulated primers and protective layers.
- Reduce reapplication costs, extending metal lifespan in harsh environments.
For businesses looking to minimise maintenance costs while maximising protection, choosing the right coating system—backed by proper surface preparation—makes all the difference.
5. The Game-Changer: Metal Treatment Chemicals That Prevent Corrosion at the Root
Protective coatings act as a shield, but what happens when corrosion starts before the coating is even applied? That’s where metal treatment chemicals make a difference. These solutions don’t just cover metal—they chemically alter its surface, making it naturally more resistant to corrosion.
Why Coatings Fail Without Proper Surface Treatment
Even the best coatings can fail if the metal beneath isn’t prepared correctly. Three common issues:
- Peeling & Blistering – Coatings lose adhesion when applied to an untreated or contaminated surface.
- Rust Beneath the Paint – A sign that corrosion had already started before coating application.
- Structural Weakness Over Time – Corrosion inside microscopic crevices spreads undetected, compromising strength.
A well-prepped surface is the foundation of long-lasting corrosion protection, and industries that rely on Chembond Material Technologies’ metal treatment solutions often see extended coating life and reduced maintenance needs. Phosphate coatings, rust converters, and passivation treatments all play a crucial role in strengthening metal before coatings are applied, preventing corrosion at its root.
6. The Little-Known Power of Cathodic Protection in High-Corrosion Environments
Some corrosion prevention methods act after the damage has started, but cathodic protection works differently—it prevents metal from corroding in the first place by using electrochemical principles. This technique is essential for pipelines, underground storage tanks, marine structures, and industrial facilities where moisture, chemicals, and harsh conditions accelerate corrosion.
How Cathodic Protection Works
Cathodic protection stops corrosion by turning metal structures into the cathode of an electrochemical cell, preventing oxidation. There are two widely used methods:
- Sacrificial Anode Systems – More reactive metals (like zinc, magnesium, or aluminium) corrode instead of the protected structure.
- Impressed Current Systems – A controlled electrical current prevents metal loss, ideal for large structures like pipelines and offshore platforms.
When is Cathodic Protection the Most Cost-Effective Choice?
While coatings and chemical treatments work well in many cases, they can be damaged, wear off, or require frequent reapplication. Cathodic protection becomes a cost-effective solution in environments where:
✔ Constant exposure to moisture and chemicals accelerates corrosion (e.g., oil refineries, water treatment plants).
✔ Metal parts are difficult to inspect or recoat, such as underground or submerged structures.
✔ Long-term asset protection is a priority—properly installed systems can last decades with minimal upkeep.
Many industries pair cathodic protection with coatings and chemical treatments for multi-layered defence. Companies using solutions like Chembond Material Technologies’ corrosion inhibitors alongside cathodic protection often achieve extended service life with lower maintenance costs.
Skipping cathodic protection in the wrong environment isn’t just risky—it can turn a small corrosion issue into a million-rupee repair problem.
7. Are You Designing for Corrosion Prevention or Just Hoping for the Best?
Many businesses invest in high-quality coatings and metal treatments but overlook design flaws that accelerate corrosion. The way metal components are shaped, assembled, and positioned plays a crucial role in how long they last before corrosion sets in.
Common Design Mistakes That Lead to Faster Corrosion
- Trapped Moisture and Poor Drainage
- Issue: Water pooling in small crevices or horizontal surfaces speeds up corrosion.
- Solution: Design components with proper drainage and avoid sharp corners where moisture collects.
- Galvanic Corrosion from Mixed Metals
- Issue: When two different metals are in contact, one corrodes faster due to electrical potential differences.
- Solution: Use compatible metals or apply insulating coatings between dissimilar materials.
- Welded Joints Without Proper Coating
- Issue: Welded areas are more prone to corrosion due to high heat exposure and microstructural changes.
Solution: Use post-weld treatments like passivation or protective coatings to reinforce these areas.
Small Design Tweaks That Can Save Lakhs in Repairs
✔ Opt for rounded edges instead of sharp corners, which trap moisture.
✔ Use corrosion-resistant fasteners to prevent weak points in assemblies.
✔ Ensure uniform coating coverage, especially in hard-to-reach areas.
Many manufacturers using Chembond Material Technologies’ pre-treatment solutions integrate these design strategies early, ensuring coatings bond better and metal structures last longer.
Designing for corrosion prevention isn’t an afterthought—it’s one of the easiest, most cost-effective ways to extend metal lifespan without extra spending.
8. How Chembond Material Technologies Helps Industries Stay Ahead of Corrosion
Corrosion protection isn’t a one-size-fits-all solution. Different industries face different challenges, from high-humidity environments that accelerate rust to chemical exposure that weakens metal over time. The key to cost-effective protection is selecting treatments designed for specific conditions.
Industry-Specific Corrosion Solutions That Reduce Long-Term Costs
- Metal Treatment Chemicals – Improve coating adhesion and enhance corrosion resistance.
- Protective Coatings – Formulated for extreme industrial conditions, reducing reapplication cycles.
- Specialised Corrosion Inhibitors – Used in pipelines, cooling systems, and storage tanks to prevent oxidation at the source.
Proven Results Across Industries
- Manufacturing & Automotive – Enhanced surface preparation, leading to fewer defects and lower repainting costs.
- Infrastructure & Construction – Increased metal durability in coastal and high-moisture environments.
- Oil & Gas – Stronger pipeline protection with advanced inhibitor technology, reducing maintenance shutdowns.
Many businesses spend more than necessary on corrosion control simply because they’re using generic solutions instead of targeted protection. Chembond Material Technologies provides industry-specific treatments that extend metal lifespan, reduce maintenance, and lower overall costs.
Cost-Effective Corrosion Protection Starts with the Right Choices
Corrosion weakens metal, disrupts operations, and drives up costs. Many failures can be traced back to poor surface preparation, the wrong coatings, or neglecting preventive treatments.
A well-planned approach reduces maintenance, extends equipment life, and prevents expensive repairs. The goal isn’t to spend more—it’s to choose protection that lasts.
At Chembond Material Technologies, we provide metal treatment chemicals, high-performance coatings, and corrosion inhibitors designed for real industrial conditions.
Protecting metal assets doesn’t have to be complicated. Get in touch to find the right solution for your company.