Rust, chemicals, and wear can destroy structures faster than you expect. Without the right coating, even the sturdiest materials fail. Protecting surfaces isn’t just about looks—it’s about keeping your projects safe, strong, and cost-effective.
Choosing the right industrial coating is tricky with so many options. Some coatings shield against moisture, while others fight corrosion or heat. A wrong choice can lead to early failures, costly repairs, and unnecessary downtime.
We understand the challenges you face in construction and manufacturing. Our coatings provide durable, high-performance protection tailored to Indian conditions. Let’s explore the best solutions to keep your projects secure and long-lasting.
Common Types of Industrial Coatings
Every coating has a role, ensuring durability and protection in different settings. Epoxy coatings, for example, are the go-to for industrial floors and machinery due to their incredible strength and resistance to chemicals. They create a hard, protective layer that’s tough enough for heavy machinery.
Polyurethane coatings, on the other hand, are known for flexibility and weather resistance. They hold up well against abrasion, making them ideal for surfaces exposed to impact and UV light. Alkyd coatings, commonly found in metal and wood applications, dry through oxidation to provide long-lasting protection.
For areas prone to rust, zinc-rich coatings are the ultimate defense. These coatings work like a sacrifice, corroding before the metal they protect. By doing so, they extend the life of steel structures, ensuring bridges, pipelines, and industrial equipment remain in working condition.
Here are the most common types of industrial coatings and their uses.
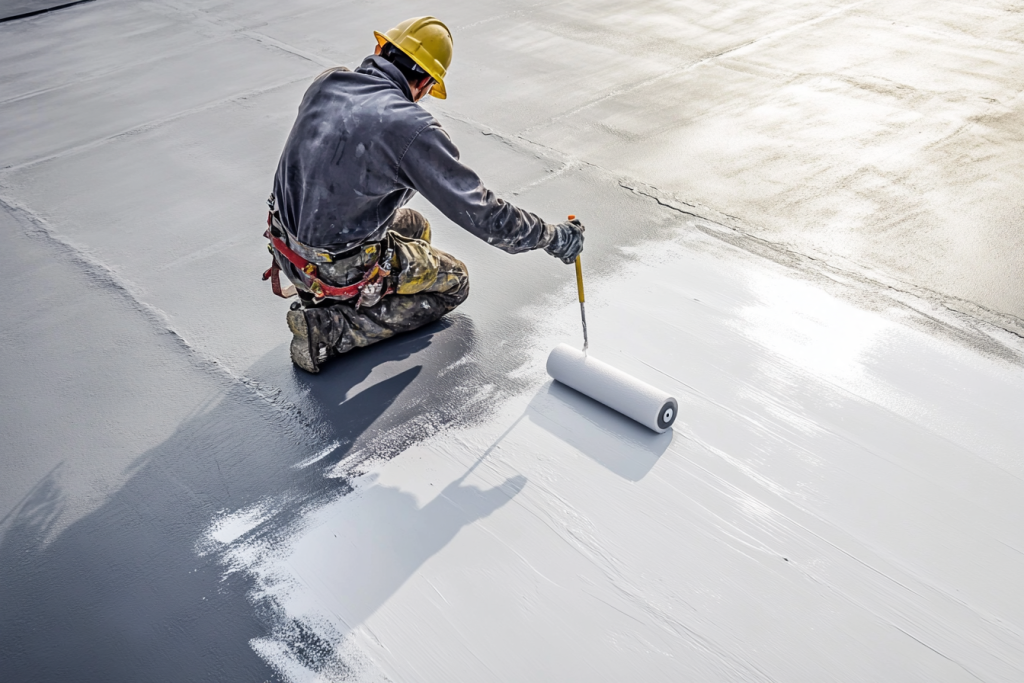
1. Epoxy Coatings
Epoxy coatings are widely used for their excellent adhesion, chemical resistance, and durability. They form a hard, protective surface that withstands heavy traffic and harsh environments. Common applications include:
- Floor coatings in warehouses and factories
- Protective layers on pipelines and tanks
- Marine and offshore structures
2. Polyurethane Coatings
Polyurethane coatings offer flexibility and UV resistance, making them ideal for exterior surfaces exposed to sunlight and weathering. These coatings are commonly used for:
- Automotive finishes
- Industrial machinery
- Bridges and steel structures
2. Polyurethane Coatings
Polyurethane coatings offer flexibility and UV resistance, making them ideal for exterior surfaces exposed to sunlight and weathering. These coatings are commonly used for:
- Automotive finishes
- Industrial machinery
- Bridges and steel structures
3. Acrylic Coatings
Acrylic coatings provide fast-drying protection with excellent color retention. They are often used in applications requiring a balance between aesthetics and durability. Common uses include:
- Architectural structures
- Road markings
- Industrial equipment
4. Alkyd Coatings
Alkyd coatings are oil-based and known for their excellent adhesion and gloss retention. These coatings are suitable for:
- Metal surfaces in industrial environments
- Machinery and equipment
- Structural steel and pipes
5. Zinc-Rich Coatings
Zinc-rich coatings are designed to provide corrosion resistance by acting as a sacrificial layer. They protect steel structures from rust and oxidation. Typical applications include:
- Bridges and transmission towers
- Marine vessels and offshore rigs
- Reinforcement bars in concrete structures
6. Fluoropolymer Coatings
Fluoropolymer coatings are highly resistant to chemicals, heat, and corrosion. They are commonly found in:
- Non-stick cookware
- Chemical processing plants
- Aerospace components
7. Ceramic Coatings
Ceramic coatings offer extreme heat resistance and durability. These coatings are used in:
- High-temperature industrial equipment
- Exhaust systems and engine components
- Aerospace and military applications
8. Powder Coatings
Powder coatings are applied as a dry powder and cured under heat, resulting in a durable and environmentally friendly finish. These coatings are ideal for:
- Metal furniture
- Appliances and automotive parts
- Outdoor structures
Specialised Industrial Coatings
Some coatings are built for extreme environments. Intumescent coatings, for instance, expand when exposed to heat, forming a charred barrier that slows the spread of fire. These coatings are essential in fireproofing buildings, warehouses, and steel structures.
Ceramic coatings stand up to high temperatures, making them perfect for furnaces, exhaust systems, and even aerospace components. Their heat resistance helps prevent material breakdown in extreme conditions. Fluoropolymer coatings, widely used in chemical plants, offer low friction and excellent resistance against corrosive substances.
For surfaces facing constant weather exposure, polysiloxane coatings provide lasting durability. They hold up against UV rays, moisture, and harsh environmental conditions, making them ideal for offshore structures and industrial facilities that endure heavy wear.
Industrial Coatings for Different Materials
Steel, concrete, and plastic each require different coatings to ensure longevity. For steel, corrosion-resistant coatings help prevent rust and structural weakness. Coatings for stainless steel offer both protection and aesthetics, creating a polished, durable finish.
Concrete structures benefit from sealants that prevent water absorption and chemical damage. Without proper protection, concrete can crack or weaken over time. In coastal and marine environments, specialized coatings prevent saltwater corrosion on docks, ships, and offshore platforms.
Even plastic and composite materials need coatings for added protection. Some coatings enhance durability, while others improve appearance, offering an extra layer against wear and tear. Selecting the right coating ensures materials stay strong and functional, regardless of their environment.
Industrial Coatings for Different Materials
Steel, concrete, and plastic each require different coatings to ensure longevity. For steel, corrosion-resistant coatings help prevent rust and structural weakness. Coatings for stainless steel offer both protection and aesthetics, creating a polished, durable finish.
Concrete structures benefit from sealants that prevent water absorption and chemical damage. Without proper protection, concrete can crack or weaken over time. In coastal and marine environments, specialized coatings prevent saltwater corrosion on docks, ships, and offshore platforms.
Even plastic and composite materials need coatings for added protection. Some coatings enhance durability, while others improve appearance, offering an extra layer against wear and tear. Selecting the right coating ensures materials stay strong and functional, regardless of their environment.
Applications of Industrial Coatings in Various Sectors
Industrial coatings keep cars, ships, and aircraft in top shape. Automotive coatings protect against scratches, rust, and environmental damage. These coatings ensure vehicles stay looking new while improving durability.
In the marine sector, coatings safeguard ships from constant exposure to saltwater. Without proper protection, corrosion can eat away at metal surfaces, weakening vessels over time. The same applies to offshore structures, where coatings must endure extreme marine conditions.
Manufacturing plants use coatings to prolong the life of machinery. Whether it’s reducing friction, defending against chemicals, or improving heat resistance, coatings enhance equipment performance. In aerospace, specialized coatings withstand extreme temperatures and pressures, ensuring aircraft perform safely at high altitudes.
Factors to Consider When Choosing an Industrial Coating
Industrial coatings keep cars, ships, and aircraft in top shape. Automotive coatings protect against scratches, rust, and environmental damage. These coatings ensure vehicles stay looking new while improving durability.
In the marine sector, coatings safeguard ships from constant exposure to saltwater. Without proper protection, corrosion can eat away at metal surfaces, weakening vessels over time. The same applies to offshore structures, where coatings must endure extreme marine conditions.
Manufacturing plants use coatings to prolong the life of machinery. Whether it’s reducing friction, defending against chemicals, or improving heat resistance, coatings enhance equipment performance. In aerospace, specialized coatings withstand extreme temperatures and pressures, ensuring aircraft perform safely at high altitudes.
Challenges and Best Practices in Industrial Coating Application
Applying industrial coatings requires a well-prepared surface. Poor preparation leads to peeling, bubbling, or weak adhesion. Cleaning, sanding, or priming ensures the coating bonds effectively for lasting protection.
Coatings can be applied through spraying, dipping, rolling, or brushing. Each method comes with its advantages. Spraying allows for even coverage, while dipping is practical for small components. Rolling works well for large flat surfaces, and brushing helps with detailed areas.
Ensuring uniform coverage prevents weak spots that can lead to early wear. Proper curing time also matters—rushing the process can reduce coating effectiveness. Addressing common coating failures early prevents costly repairs later.
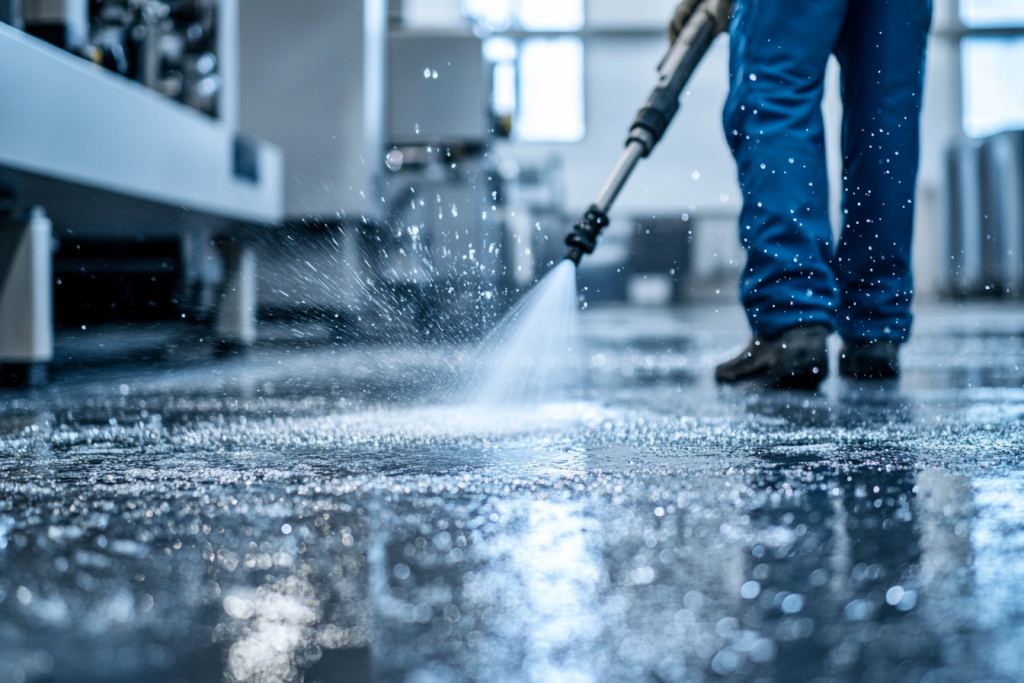
Protection That Lasts: Get Coatings That Stand the Test of Time
When it comes to industrial surfaces, wear and tear is inevitable. Harsh weather, chemicals, and daily use can take their toll, making protection a necessity, not a choice. A strong, reliable coating keeps your infrastructure safe, reducing costly damage and ensuring everything stays in top condition.
The right coating does more than just cover a surface. It seals, strengthens, and extends the life of your structures, saving you from frequent repairs. Choosing wisely means fewer maintenance headaches and long-term durability, making it an investment that pays for itself.
At Chembond Material Technologies, we provide advanced protective coatings for industrial and infrastructure projects. Let’s help you find the best solution for lasting protection—reach out to us today.
FAQs
What are the main types of industrial coatings?
How do I choose the best industrial coating for my application?
Consider the environment, exposure to chemicals, moisture, or heat, and balance cost with long-term performance needs.
What are the common challenges in industrial coating application?
Poor surface preparation, uneven application, and inadequate curing time can lead to peeling, bubbling, or reduced protection.
How do coatings improve the lifespan of industrial materials?
By shielding surfaces from corrosion, abrasion, and environmental factors, coatings help materials last longer with minimal maintenance.