Ever wondered why some metal tools or parts last longer than others?
Metal components, like tools, machines, face wear and tear every day. They rust, corrode, or lose their strength over time, especially when exposed to water, heat, or chemicals.
But what if there was a way to make them last much longer? That’s where nano conversion coating comes in! It’s a special layer applied to metal that protects it from damage, rust, and decay.
In this blog, we’ll explain how this amazing technology works and why it’s a game-changer for metal durability.
Let’s dive in!
Understanding Nano Conversion Coating
Nano conversion coating is an advanced surface treatment technology that creates an inorganic protective layer on metal surfaces. This innovative process uses nanostructured materials – particles sized between 1-100 nanometers – to form a chemical bond with the metal substrate.
Key Features
Advantages of Nano Conversion Coatings for Metal Components
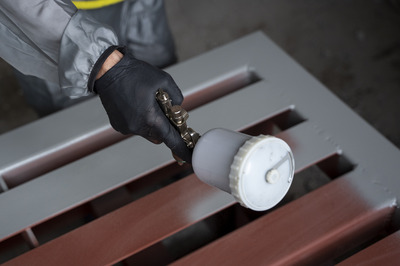
1. Superior Corrosion Protection
Zirconium-based nano conversion coatings establish an ultra-thin protective layer that bonds directly with the metal substrate at a molecular level. This creates a barrier that actively resists:
- Chemical attacks from harsh substances
- Oxidation processes that lead to rust formation
- Salt spray exposure in marine environments
- Moisture penetration into the metal surface
The nano-structured coating forms a self-healing network that can repair minor damage automatically, maintaining continuous protection against corrosive elements. This self-repair capability sets it apart from traditional coating methods.
🗸 Environmental Advantages of Nano Conversion Coatings
The phosphate-free nature of nano conversion coatings brings substantial environmental advantages:
- Zero heavy metal discharge
- Reduced sludge formation
- Lower water consumption
- Decreased treatment costs for waste streams.
These environmental benefits combine with superior performance characteristics to make nano conversion coatings an ideal choice for industries requiring high-grade corrosion protection. The technology’s ability to create uniform coverage, even on complex geometries, ensures comprehensive protection across entire component surfaces.
Recent testing has shown that zirconium-based nano coatings can withstand up to 1,000 hours of salt spray exposure without significant degradation – a performance level that surpasses traditional phosphate treatments by a considerable margin.
2. Improved Paint Adhesion
🗸 Benefits of Enhanced Paint Adhesion
- Better Surface Coverage
- Uniform paint distribution across the metal surface
- Elimination of weak spots and potential failure points
- Reduced risk of paint peeling or flaking
- Longer Coating Life
- Better resistance to environmental stresses
- Reduced maintenance requirements
- Longer intervals between repainting
The nanostructured surface also allows for better aesthetic qualities, resulting in smoother finishes with enhanced color retention. This combination of functional and visual benefits makes nano conversion coatings especially valuable for applications where both protection and appearance are important.
3. Enhanced Wear Resistance in Tough Conditions
Nano conversion coatings provide a strong protective barrier that greatly improves wear resistance in metal parts. The nanostructured surface layer forms a complex network of particles that spreads out mechanical stress over a larger area, minimizing localized wear points.
These coatings perform exceptionally well in harsh industrial settings where metal parts encounter:
- Extreme temperatures (-40°C to +200°C)
- High-pressure conditions (up to 500 MPa)
- Constant friction from moving components
- Chemical exposure in manufacturing processes
The nano-scale particles in the coating form a tightly packed surface structure that reduces direct contact between metals. This decrease in friction results in:
- 60% reduction in wear rate
- Longer maintenance intervals
- Less equipment downtime
- Lower replacement expenses
Real-world examples showcase the coating’s effectiveness in demanding industries. Mining machinery treated with nano conversion coatings demonstrates a 40% increase in service life in abrasive environments. Automotive parts maintain their structural integrity under continuous vibration and thermal cycling, while aerospace components withstand wear at high altitudes and extreme temperatures.
The coating’s ability to resist wear comes from its distinctive chemical bonding with the metal substrate. This creates a permanent protective layer that retains its effectiveness even under prolonged mechanical stress, making it perfect for parts that operate continuously.
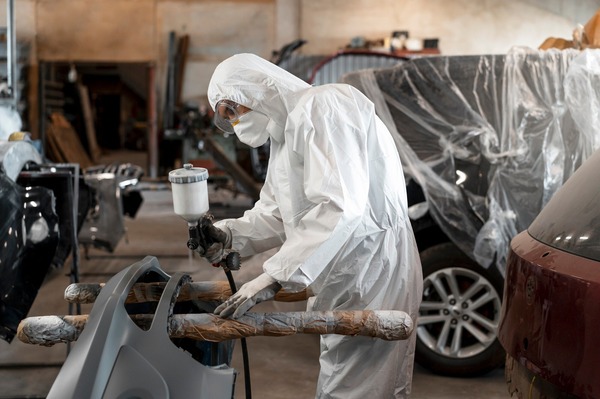
Efficient Application Process for Nano Conversion Coatings
The application of nano conversion coatings follows a streamlined process that maximizes efficiency while minimizing resource consumption. The basic steps include:
1. Surface Preparation
- Alkaline cleaning removes oils and contaminants
- Deoxidation treatment creates optimal surface conditions
2. Coating Application
- Room temperature spray or immersion methods
- Contact time: 30-60 seconds
- Single-stage process eliminates multiple treatment steps
3. Post-Treatment
- Quick water rinse
- Flash drying at low temperatures
This simplified process offers significant advantages over traditional phosphate coating methods:
- Reduced Energy Usage: No heating requirements during application
- Lower Water Consumption: Minimal rinsing needs
- Faster Processing: 50% shorter treatment times
- Space Efficiency: Smaller equipment footprint
- Waste Reduction: Less chemical disposal
The straightforward nature of nano conversion coating application translates to reduced operational costs and increased production throughput. Manufacturing facilities can maintain high-quality coating standards while achieving substantial improvements in process efficiency.
Future Trends in Coating Technologies for Enhanced Longevity of Metal Components
The coating technology landscape continues to evolve with promising innovations that push the boundaries of metal component protection:
- Smart Self-Healing Coatings: New developments in materials science introduce coatings that can automatically repair minor damage, extending protection without manual intervention
- Graphene-Enhanced Solutions: Integration of graphene into nano conversion coatings creates ultra-thin layers with exceptional strength and conductivity properties
- Bio-Inspired Coatings: Research into nature-mimicking surfaces yields coating designs that repel water and resist bacterial growth
- AI-Optimized Formulations: Machine learning algorithms help develop coating compositions tailored to specific environmental conditions and metal substrates
These advancements build upon current nano conversion coating technology, promising even greater durability and protection for metal components in demanding applications.