Phosphating, also called phosphate coating, is a process that the oil and gas sector must use if it wants to improve metal surfaces’ durability. This blog post aims to provide an insightful but detailed technical inspection of phosphating, highlighting its advantages and different types employed across industries.
What is Phosphating?
Phosphating is a way of transforming metal surfaces into metal with phosphate crystals that cannot dissolve. This layer eventually makes it possible for more paint or powder particles to adhere well to it and has better anti-corrosion properties. The method entails dipping metal into a phosphoric acid solution, thus resulting in the creation of a layer of phosphate through chemical reactions.
Benefits of Phosphating
Phosphating offers several benefits crucial for maintaining the integrity and performance of metal components in harsh environments.
Corrosion Resistance:
When the phosphate layer created from phosphating is applied to the metal surface, it serves as a powerful barrier against environmental elements such as salt, moisture, or chemicals. This is usually done to minimise the chances of corrosion or rusting, preventing metals from deteriorating and thus making them last longer.
Improved Paint Adhesion:
The phosphate coating provides an amazing foundation for the coming paint processes. It improves paints’ and coatings’ adhesion properties, resulting in more effective bonding to a metal surface. As a consequence, it becomes possible to create finishes that last longer since they do not require continuous repainting or maintenance.
Enhanced Wear Resistance:
The existence of a phosphate coating makes subsequent paint applications easier. Enhancing paint adhesion properties makes the bonds between them and the metal surface more effective. This enhances the life of the paint and makes the surface more durable, so there is little need for frequent repainting or maintenance.
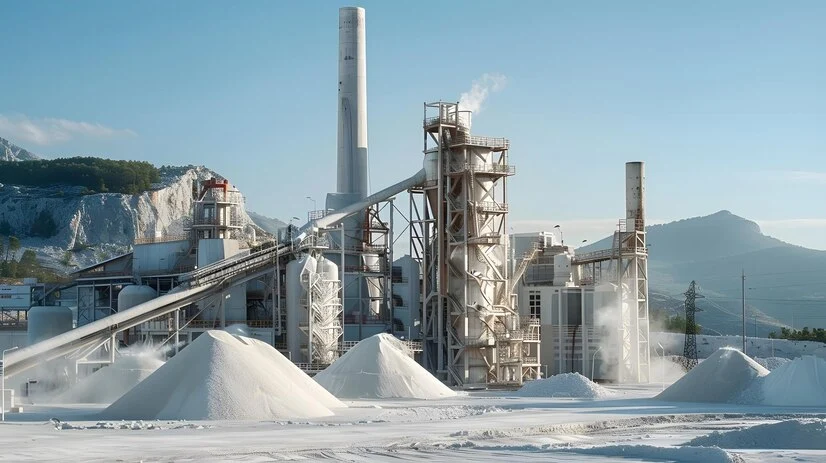
Cost-Effective Pretreatment:
Compared to other corrosion protection methods, phosphating is relatively inexpensive. It offers a cost-effective solution for enhancing metal surfaces before painting or coating, making it an attractive option for industries looking to balance performance and budget considerations.
Improved Lubricity:
Phosphate coatings, particularly manganese phosphating, can enhance the lubricity of metal surfaces. This is crucial in applications where reducing friction between metal parts is essential, such as in automotive and machinery components. Improved lubricity leads to smoother operation and less wear on parts.
Surface Preparation:
Phosphating is an excellent method for preparing metal surfaces for further processing. It cleans and activates the metal surface, making it more receptive to additional treatments like painting, powder coating, or plating. This ensures better coating performance and adherence, producing a superior final product.
Versatility in Applications:
Phosphating can be applied to a wide range of metals, including steel, iron, and aluminium. This versatility makes it suitable for various industries, from automotive and aerospace to construction and consumer goods. It can be tailored to specific needs, such as zinc phosphating for paint adhesion or manganese phosphating for wear resistance.
Environmental and Safety Benefits:
Modern phosphating processes have been developed to be more environmentally friendly and safer for workers. Many formulations now use less toxic chemicals and produce less hazardous waste, aligning with stricter environmental regulations and improving workplace safety.
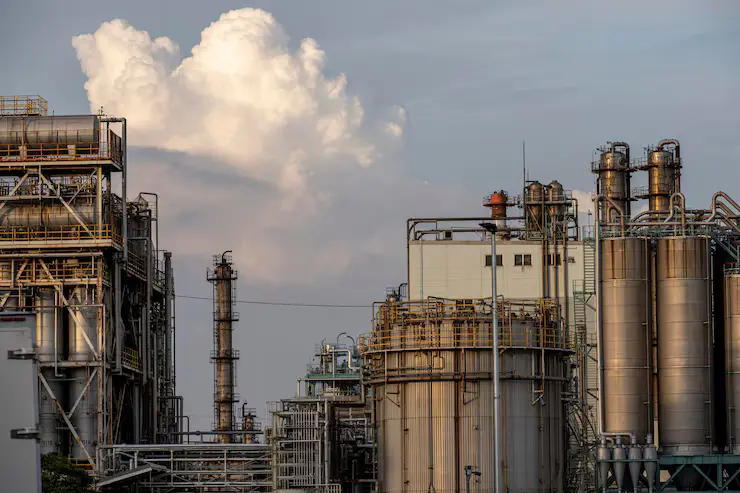
The Phosphating Process
The phosphating process generally involves several stages: cleaning, rinsing, phosphating, and post-treatment. Each stage is critical to ensuring the coating’s effectiveness.
🗹 Cleaning:
Removing any contaminants from the metal surface to ensure proper adhesion of the phosphate layer.
🗹 Rinsing:
Eliminating any residual cleaning agents.
🗹 Phosphating:
Immersing the metal in a phosphoric acid solution to create the phosphate layer.
🗹 Post-Treatment:
Applying additional treatments, such as sealing, to enhance corrosion resistance.
Enhance Your Metal Protection with Chembond ChemBondMatech
At Chembond Matech, we specialise in advanced phosphating solutions for metal surfaces that ensure superior corrosion resistance, improved paint adhesion, and extended wear resistance.